needle pinhole of aluminum foil
needle pinhole is the main defect in raw materials, aluminum foil material on the roll, rolling oil, the size of the dust in the air even reached about 6 microns into the roll gap will cause the pinhole, so there was no 6 microns aluminum foil pinhole is impossible, can be evaluated with the number and size it due to the improvement of aluminum foil rolling conditions, especially the dust and rolling oil filter effectively and convenient roll changing system Settings, aluminum foil pinhole number more and more dependent on the metallurgy quality and the processing defects of raw material.
uneven roll printing disadvantages of aluminum foil production
It is mainly roll caused by aluminum foil defects, into point, line, surface three.The most prominent features appear in three cycles.The main causes of this defect are: improper grinding of roll;Foreign material damage roll: imprinted defect roll;Roll fatigue;Roll bump, slip, etc.All the factors that can cause the surface damage of roll can harm the rolling of aluminum foil.Because the aluminum foil rolling roller surface smoothness is very high, slightly uneven luster will affect its surface state.Regular cleaning of the rolling mill, keep the mill clean, ensure the normal work of the roller cleaner, regular roll change, reasonable grinding, are the basic conditions to ensure the uniform surface of aluminum foil rolling.
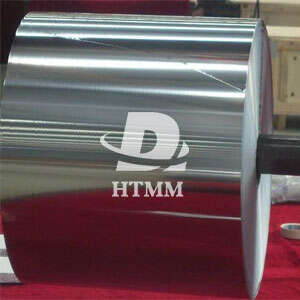
Due to the serious shape defects, when the aluminum foil is rolled or unfolded, it will form wrinkles, whose essence is that the tension is not enough to flatten the foil.For the device with a tension dimension of 20MPa, the shape of foil shall not be greater than 30I, and when it is greater than 30I, it will inevitably wrinkle.Due to the rolling aluminum foil is often subjected to more tension than the subsequent processing, some in the rolling only for poor shape, including improper roll grinding, roll shape is wrong, incoming material poor shape and improper adjustment of the shape.
Aluminum foil bright spots, bright marks
The bright spot and bright mark caused by the improper use of shuanghe oil on the aluminum foil, mainly because of the insufficient strength of shuanghe oil film, or uneven rolling deformation caused by uneven roll surface, the appearance is like hemp skin or foreign body pressing.It is an effective measure to solve this kind of defect to choose reasonable double compound oil, keep the material clean and roll surface even.Of course, it is necessary to change the pressure and choose good aluminum plate.
aluminum foil's oil pollution
Grease refers to the excess oil on the surface of aluminum foil after rolling, that is, in addition to the rolling oil film.These oils are often by the roll neck or mill outlet on, below the swing, splash, drop on the foil surface, and more dirty, complex composition.The oil pollution on the surface of aluminum foil is more harmful than other rolled materials. Firstly, as the finished aluminum foil is mostly used as decoration or packaging material, it must have a clean surface.Second, its thickness is thin, easy to form bubble in the annealing of the back channel, and because of the amount of oil in the formation of too much residue and affect the use.How much oil pollution defect is an important index to evaluate the quality of aluminum foil.
Although there are many kinds of defects in aluminum foil rolling, they are mainly manifested as: pinhole, roll eye, slit and air passage characterized by holes;Oil stains, uneven luster, vibration marks, tension lines, water spots and bright spots characterized by surface conditions;To influence the plate shape, wrinkling, discounting and improper winding of the post-processing process;Thickness differences characterized by size, etc.