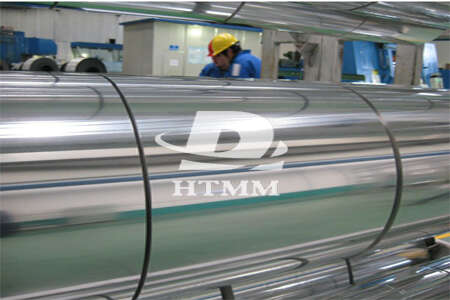
Aluminum foil, especially double zero Aluminium foil, is becoming a common commodity, a standardized product with increasingly strict requirements and mature technology.
Aluminium foil production equipment has been digested and absorbed in China, thanks to the understanding and accumulation of core technology of aluminum foil production for more than 30 years.
From all angles, China has become the world's aluminum foil powerhouse. Not only has the world's largest production capacity, but also brings together the world's most advanced equipment, has accumulated the most advanced technology, and has the world's largest production enterprise.
According to the use of aluminum foil, it can be divided into: flexible aluminium foil, cardboard aluminium foil, cigarette aluminium foil, wine label aluminium foil, cable aluminium foil, medicine aluminium foil, household foil and so on. These are basically the traditional aluminum foils used for packaging. With the continuous development of science and technology, the use of aluminum foil in electronic products has also emerged, and the amount of electronic products has also increased several times each year. Such as: battery aluminum foil, electronic capacitor foil, electronic label foil, etc.
Generally, the thickness of the aluminum foil required for electronic capacitor foil is the thinnest, and the commonly used specifications are about 0.005 to 0.006 mm, which is required to be annealed.
The battery aluminum foil usually has a thickness of about 0.01 to 0.03 mm, and it is generally required to be in the H18 hard state. This product has high requirements for the appearance of aluminum foil, especially for the shape of the plate.
Electronic label foil is an aluminum foil that is used as an electronic closed circuit. The thickness is generally above 0.015mm and it is annealed. This type of product requires higher pinholes, pits, and pits in aluminum foil.
With the continuous enrichment and development of electronic products, it is believed that the application of aluminum foil in the electronic product market will become more and more extensive, and it will become a new important development trend and opportunity for the aluminum foil industry.